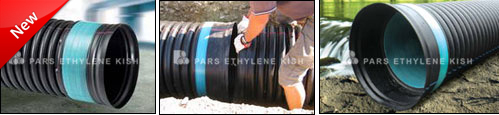
The production process of double wall corrugated pipe
Pars Ethylene Kish has come up with a unique innovation in production of corrugated pipe (double wall corrugated pipe ) and has been able to incorporate the most recent technology of the world in production of double wall corrugated pipe. The machinery used for production of double wall corrugated pipe in Pars Ethylene Kish are all made by Drossbach Maschinenbau GmbH of Germany and the production line (namely the suction machine, materials’ silo, gravimetric, extruder, corrugator, cooling tank, hauling machine, saw and other side equipment of the production line) are entirely made of German machinery.
Pars Ethylene Kish after doing lots of research and building on the knowledge of the managers and the research and development unit has managed to make a significant difference (innovative and creative) in production of double wall corrugated pipes, corrugator dies which has yielded to pipes with more resistance, higher quality and longer lifetime compared to the other samples.

The corrugated pipes manufactured by Pars Ethylene Kish company are also characterized by another property which is a protective wrapping on the coupling of double wall corrugated pipe. The wrapping, being very simple, acts as a protective belt and prevents the coupler from tapering in the junction of the pipes and also prevents fluids from permeating out. Another main defect of the corrugated pipes in the market is this very tapering and erosion of the pipes at the junction which degrades the performance of the transmission line severely.
In order to produce corrugated pipes, first the raw materials are melted at high temperature in the extruder through the extrusion process. Thermal adjustment in this stage is very important since in different thermal areas the type of the product and the polyethylene would be different (extrusion is a process in which the raw materials are poured in a die and applying pressure products with different designs are made). Then the resultant polyethylene passes through a tank and turns into the shape of a pipe. To create grooves and ridges on the outer surface of the pipe (corrugating the pips) this process is performed under vacuum situation and using rotatory and continuous dies. Thermal adjustment in this stage is important too. There are water nozzles at the end of the production line of corrugated wall for cooling of the output product. The quality control stages of the products are performed at the factory laboratory.
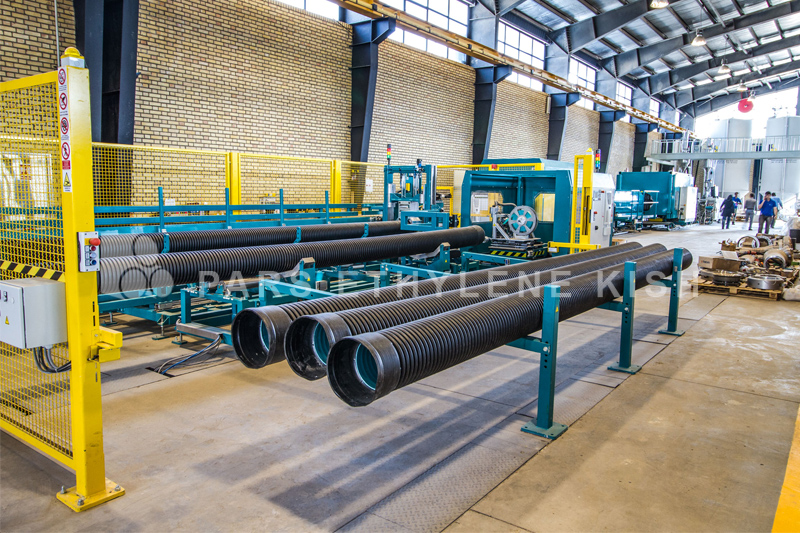
Production of corrugated polyethylene pipes is rapidly developing in technology, production process and the control while production. In addition to the abovementioned definitions, the production process of the corrugated pipes could be divided into 5 stages including:
- Preparation of the raw material
This is an important stage in the production process for it requires the collaboration of the staff in different levels. Preparation of the raw material starts with the purchase order and ends with making the mixture and transferring it to the extruder funnel. This stage is directly related to the production plans. This phase consists of: purchase order, receiving, storing and making the mixture.
Provision of the raw material:
The raw material used in the production process are approved by the employees in an operational team as production, guarantee of quality and purchase, based on technical specifications of the raw material, the required criteria for product standards, reliability of the supplier and quality control tests of the raw material and the products made from it. In case the raw material would possess the desired quality, it will be ordered and purchased.
Receiving and storing of the raw material:
The raw materials are sampled and evaluated by the quality control agent upon arrival at the factory. In case that the sent shipment was in conformity with the requested specifications based on the specs out on the specifications documents of the products and the bill of lading, the quality control agent will perform the standard tests on the samples to determine the conformity of the shipment and to provide report. In case of any discrepancy in the specifications of the raw material with the relevant standards, the shipment will be returned.
The tests performed on the raw materials are as follows:
- melt flow index (MFI)
- density test
- oxidative induction times (OIT)
- Humidity test
- soot dispersion test
- Extrusion
In the extrusion stage of thermoplastics, the polymers are melted by the heat created inside the extruder. Melting of heavy polyethylenes is controlled by precise adjustment of the thermal profile in different areas based on the polymer type which results in optimum pressure in the extruder output. This task is performed by the production personnel according to the guidance instructions for quality control and method.
- Corrugation
After the extrusion, the polyethylene has passed through die and gets the pipe shape at the die output. Then the corrugating process of outer surface of the double wall pipe is performed by applying die and vacuum, while the inner surface of the pipe is still smooth. Such molding process is continuously performed by corrugating rotary dies.
Based on type of the desired pipe, respective parts and dies are installed on the production line and during the production process, stabilization of thickness of polyethylene pipe layers, production speed and temperatures are adjusted at their optimum. The quality control agent performs the necessary controls on the final products to ensure the desired quality is achieved.
- Calibration
The cooling stage is essential for stabilization of the dimension in production of plastic pipes which is named as calibration and is different based on the pipe thickness and production speed. In order for cooling of the pipes, the water nozzles are used which are embedded all around the pipe along the calibrator. The water temperature of the cooling system is also under control.
- Confirmation and final product tests
In the final stage of the production process, the corrugated pipe is sampled and the quality control unit performs the respective tests to determine whether the final product is in conformity with the required specification and also optimizes the adjustments.
The production process, the stages from stage 2 to 5 are controlled by the production personnel and quality control agent. Finally, the quality control unit samples the products and does the final confirmation according to the standard tests.
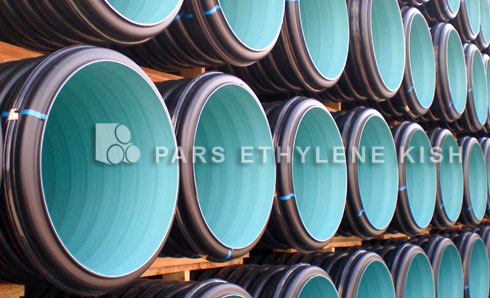
Corrugated pipes are the most commonly used pipes for collection and transmission of sewages in Iran and also other countries in the world. The international standard insists on production of corrugated pipes with mechanical resistance of 16 to 31.5 Newton per meters squared. In Iran, corrugated pipes must have a mechanical resistance of 31.5 newton per meters squared. All inspectors insist that the mechanical resistance of the corrugated pipe manufactured by any company must be equal to 31.5 newton per meters squared in the first place.
Corrugated pipes could be found in the following sizes in millimeters:
110 mm corrugated pipe, 125 mm corrugated pipe, 160 mm corrugated pipe, 200 mm corrugated pipe, 250 mm corrugated pipe, 315 mm corrugated pipe, 400 mm corrugated pipe, 500 mm corrugated pipe, 600 mm corrugated pipe, 700 mm corrugated pipe, 900 mm corrugated pipe, 1000 mm corrugated pipe, 1200 mm corrugated pipe, 1400 mm corrugated pipe, 1600 mm corrugated pipe, 1800 mm corrugated pipe, 2000 mm corrugated pipe, 2500 mm corrugated pipe
Double wall corrugated pipes are produced in different color and appearance in Pars Ethylene Kish and all contain a wrapping on the coupler which prevents tapering and hence water leakage and also increases the pipe robustness and lifetime.
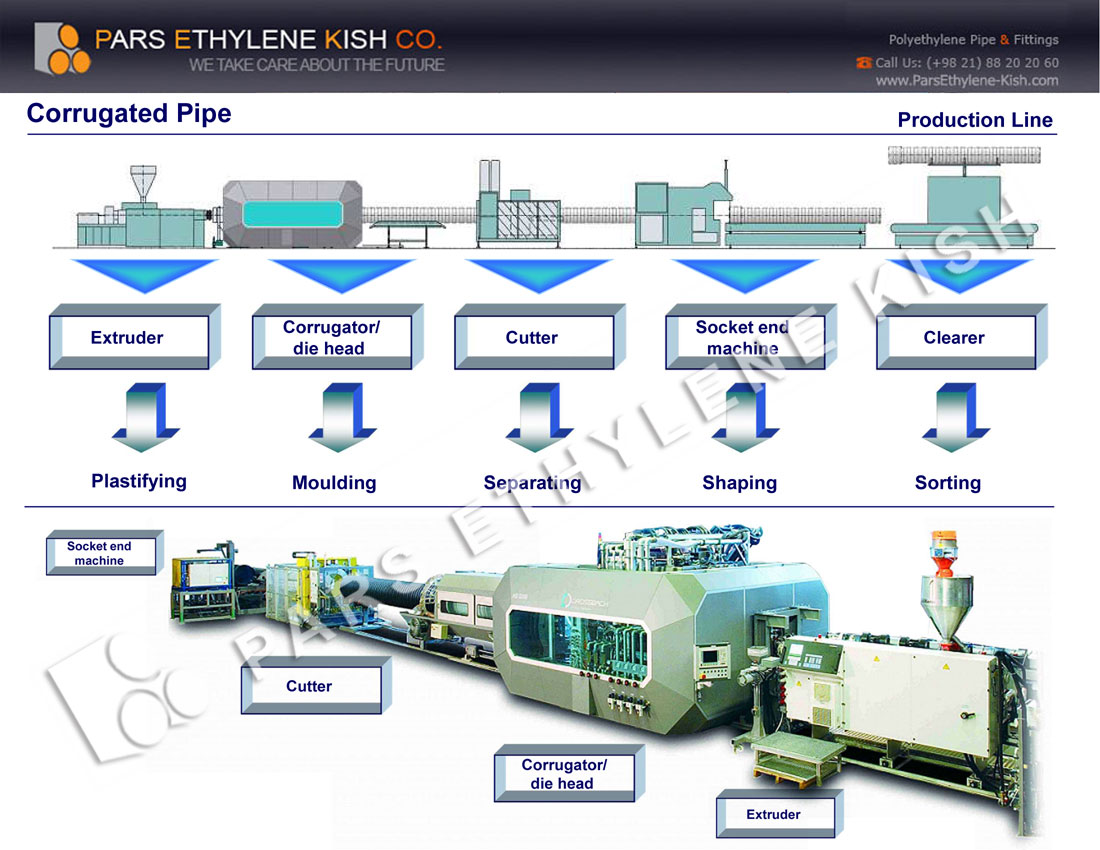
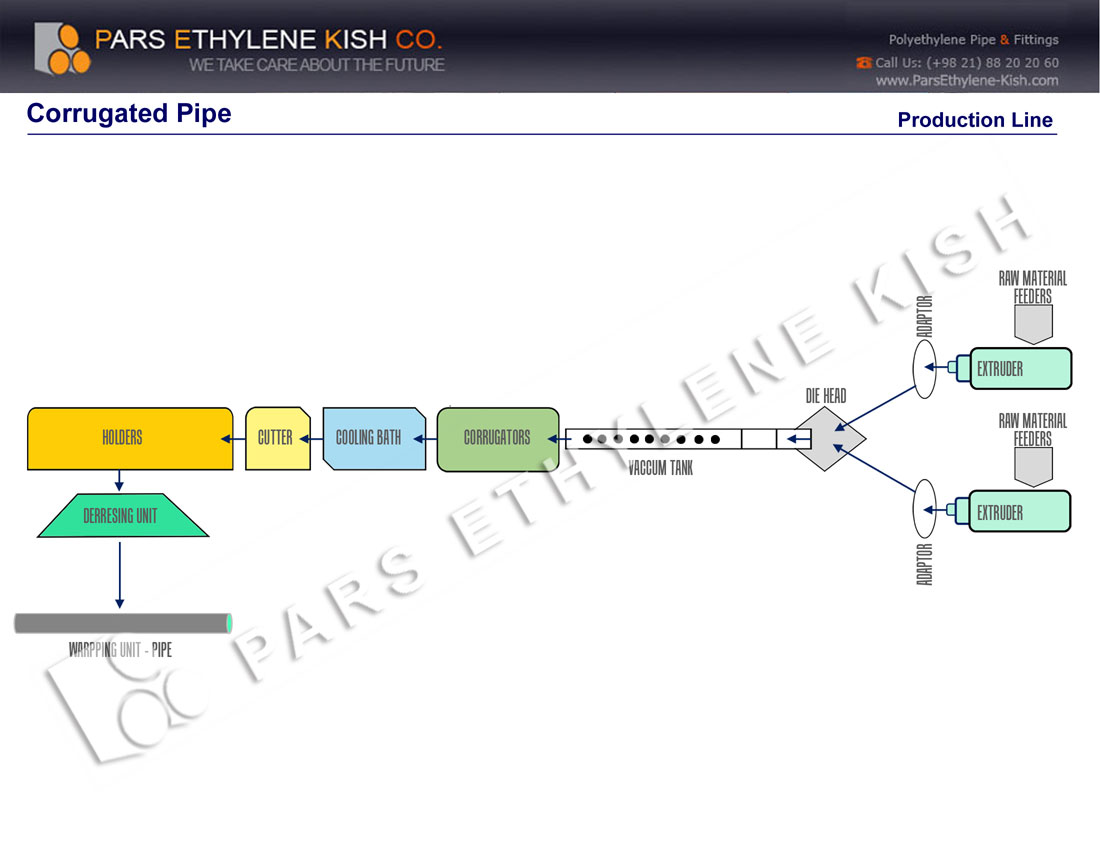
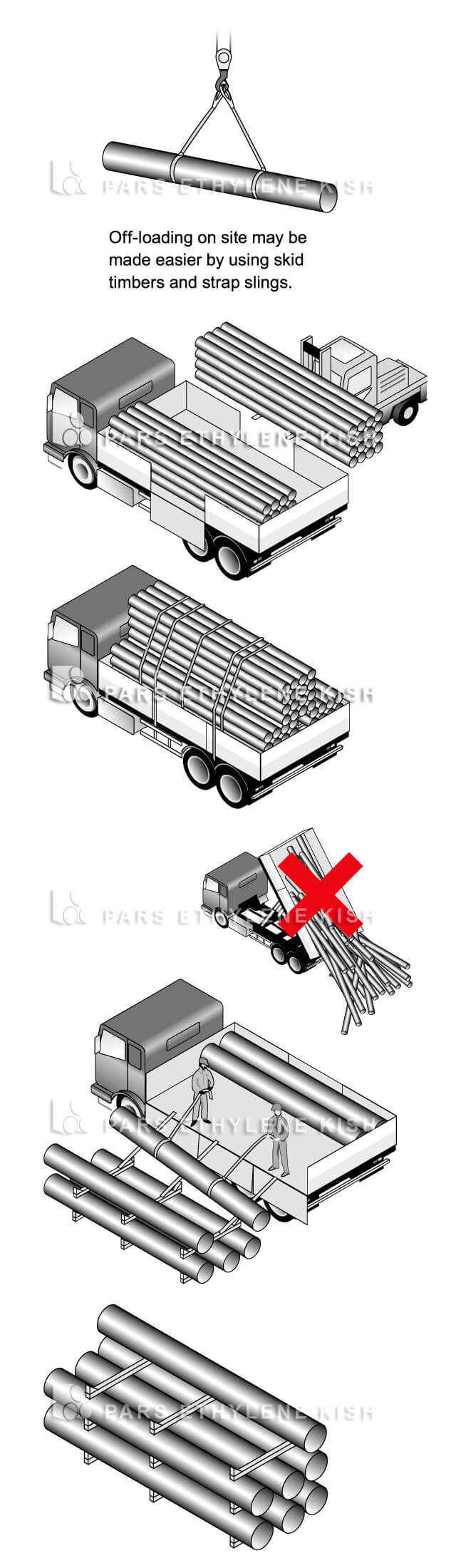

