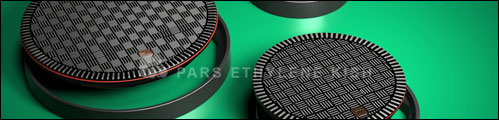
Composite Manhole Cover
Sewage Manhole Lids
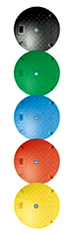
Manhole lids, especially composite ones, are widely used in oil, gas, petrochemical, water and sewage industries, telecommunications and factories. In the wake of many problems with the use of metal manhole lids, such as breakage, rusting, rotting, recyclable materials and theft, Pars Ethylene Kish Co. in Iran, and in line with the advanced world technology, manufactured composite non-metallic manhole lids with the best quality. The popularity and desire to replace the metal manhole lids with composite ones are increasing, due to the reduction in the cost of stealing cast iron lids, the high mechanical and hydraulic resistance, chemical resistance, apparent beauty (possibility to produce in different colors), resistance to corrosive sewage gases and non-erosion. Composite manhole lids come from the combination of materials, polymer resins and other chemicals.
Composite manhole covers have many advantages over traditional metal covers. They are lighter in weight, making them easier to handle and install. They are also more resistant to corrosion, which means they have a longer lifespan and require less maintenance. Additionally, they are more cost-effective in the long run since they require less frequent replacement.
Introduction
The production of composite manhole covers is a process that involves the use of resin and fiberglass materials to create durable, strong, and corrosion-resistant covers. Composite manhole covers are becoming increasingly popular due to their many advantages over traditional metal covers, including a longer lifespan, lighter weight, and lower maintenance costs. In this article, we'll take a closer look at the production process of composite manhole covers and explore the benefits they offer for infrastructure projects and public works.
Raw Materials
The production of
composite manhole covers involves the use of two primary materials: resin and fiberglass. Resin is a synthetic polymer that acts as a binding agent, while fiberglass is a reinforced plastic made of glass fibers
.
Resin is chosen for its ability to bind the fibers together and provide strength and durability to the cover. There are several types of resin used in the production of
composite manhole covers, including epoxy, vinyl ester, and polyester. Each type of resin has its own unique properties and characteristics that make it suitable for specific applications
.
Fiberglass is selected for its high strength-to-weight ratio, resistance to corrosion, and ability to withstand extreme temperatures. The fibers are typically woven into a mat or fabric, which is then impregnated with the resin during the mixing process
.
To create the mixture, the resin and fiberglass are combined in a large mixer and thoroughly blended until a homogeneous mixture is achieved. The mixing process is critical to ensure that the fibers are evenly distributed throughout the resin, creating a strong and durable composite material
.
Molding Process
After the raw materials have been mixed together, the next step in the production process of
composite manhole covers is the molding process. This involves pouring the mixture into a mold that has the shape of a manhole cover. The mold is typically made of metal and is designed to withstand the high pressure and heat required to cure the composite material
.
Once the mixture has been poured into the mold, it is closed and placed in a press. The press applies pressure and heat to the mold, causing the mixture to cure and harden into the shape of the manhole cover. The amount of pressure and heat applied during this stage is critical to ensure that the composite material has the required strength and durability to withstand the weight of vehicles and other heavy loads
.
The curing process typically takes several hours, depending on the type of resin used and the size of the manhole cover. Once the curing process is complete, the mold is opened, and the composite manhole cover is removed
.
At this stage, the composite manhole cover is still in a rough shape and requires additional finishing to ensure that it meets the required standards for strength, durability, and resistance to corrosion
.
Finishing Process
The finishing process is the final stage in the production of
composite manhole covers. It involves several steps to ensure that the cover has a smooth surface and meets the required specifications
.
The first step is to trim the cover to the proper size and shape using a saw or other cutting tool. The edges are then sanded down to remove any roughness or imperfections
.
After sanding, the cover is inspected for any defects or flaws. If any defects are found, they are repaired using a filler material that is compatible with the composite material
.
Once the cover is free of defects, it undergoes a final inspection to ensure that it meets the required standards for strength, durability, and resistance to corrosion. This inspection typically involves various tests, including load-bearing tests, impact tests, and chemical resistance tests
.
If the cover passes the inspection, it is ready to be painted or coated with a protective layer to enhance its resistance to corrosion and UV damage
.
The finished
composite manhole cover is now ready for use and can be transported to its final destination. Because of its lighter weight and easier handling, installation of composite manhole covers is typically faster and less expensive than traditional metal covers. Additionally, the longer lifespan and lower maintenance costs make them a cost-effective choice for infrastructure projects and public works
.
Advantages of composite sewage manhole lids
There are several advantages to using
composite manhole covers over traditional metal covers
:
-
Lighter weight: Composite manhole covers are significantly lighter than traditional metal covers, making them easier to handle and install. This can reduce labor costs and improve efficiency in the installation process.
-
Resistance to corrosion: Composite materials are highly resistant to corrosion, making them ideal for use in areas with high levels of moisture or chemicals. They do not rust, corrode, or degrade over time, resulting in a longer lifespan and lower maintenance costs.
-
Longer lifespan: Composite manhole covers have a longer lifespan compared to traditional metal covers. They are highly durable and can withstand heavy loads and traffic, resulting in reduced replacement costs over time.
-
Lower maintenance costs: Because composite manhole covers are resistant to corrosion and degradation, they require less maintenance than traditional metal covers. This can result in significant cost savings over time.
-
Cost-effective in the long run: Although composite manhole covers may have a higher upfront cost compared to traditional metal covers, their longer lifespan and lower maintenance costs make them a cost-effective choice in the long run.
-
Being anti-theft due the use of non-recyclable materials
-
Resistance to corrosion and acidic decay
-
Resistance to sunlight due to the presence of anti-UV materials
-
Usability in any climate and high temperature and below zero
-
ightweight, yet resistant to high pressures
-
Color variation and design based on the principles of urban beautification principles
-
No sound while under wheel pressure
-
Leveling without displacement of the hasp
-
Production based on the logo and the name of the customer
-
Composite manhole lids are manufactured according to the BS-124 standard and tested according to the classes in the table
-
Class: A15, B125, C250, D400
-
Pressure bearing (ton): 1.5, 12.5, 25.40
Overall,
composite manhole covers offer a range of benefits that make them an attractive alternative to traditional metal covers. Their strength, durability, resistance to corrosion, and cost-effectiveness make them an excellent choice for infrastructure projects and public works
.
Applications of composite manhole lids
-
Sewage visit lid
-
Fire extinguishing
-
Meter lid
-
Tap and line lid
-
Communications lid
-
Basin lid
Size of manhole lids
In accordance with the safety requirements provided in the national and international standards, the size of the lid of all manholes, including composite, cast iron and ..., must be at least 600 mm plus a 50 mm seat (25 mm in each side) and the diameter of the lid should be 650 mm. Using standard size lids are important for leveling the size of the lids in the country.
Composite manhole lid materials
The composite manhole lid materials contain reinforcing fibers (silica), encapsulated in a matrix of thermosetting resin. These materials are molded as a single integrated structure.
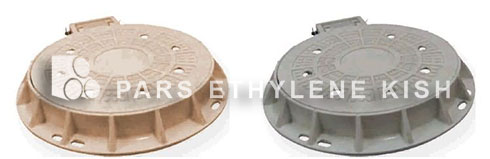
Requirements and tests for manhole composite lids
Composite lids must undergo various tests in accordance with pp. 52-56 of the standard as well. The tests are as follows:
-
Tensile modulus and stress
-
Water absorption
-
Resistance to vehicle fuel
-
Deflection under force
-
Creep resistance
-
Fatigue resistance
-
Impact resistance
-
Thermal stability
-
Surface Resistivity
-
Wear resistance
-
Permanent endurance
-
Power test
-
UV resistance
Classification of the location of composite lids
The lids are manufactured in six different classes that are selected and used according to the lid installation location in the city (pp. 14 and 15 of the Standard - Paragraphs 4 and 5). Grouping guidance based on the lid location is as follows:
-
Group 1: A15 with a tolerance of 1.5 tons for sidewalks and bike rides
-
Group 2: B125 with a tolerance of 12.5 tons for sidewalks, and parking lots
-
Group 3: C250 with a tolerance of 25 tons for the margin of the curbing maximum 0.5 m to the roadway and 0.2 m to the sidewalk
-
Group 4: D400 with a tolerance of 40 tons for roadway and main streets
-
Group 5: E600 with a tolerance of 60 tons for traffic areas and heavy vehicles, such as harbors and airports
-
Group 6: F900 with a tolerance of 90 tons for heavy-duty vehicles such as airports
To ensure the required load bearing, the lids should be tested in validated laboratories under pressure tests (in accordance with Table C.1, pp. 67 and 68 of The Standard).

Conclusion
The production of
composite manhole covers involves the use of resin and fiberglass materials to create durable, strong, and corrosion-resistant covers. The production process includes mixing the raw materials, molding the mixture into the shape of the cover, and finishing the cover to ensure that it meets the required standards for strength and durability
.
Composite manhole covers offer several advantages over traditional metal covers, including lighter weight, resistance to corrosion, longer lifespan, lower maintenance costs, and cost-effectiveness in the long run. As a result, they are becoming increasingly popular for infrastructure projects and public works
.
With their superior properties and cost-effectiveness,
composite manhole covers are a practical and sustainable solution for a wide range of applications, providing a long-lasting and durable solution that can withstand heavy loads and extreme conditions
.
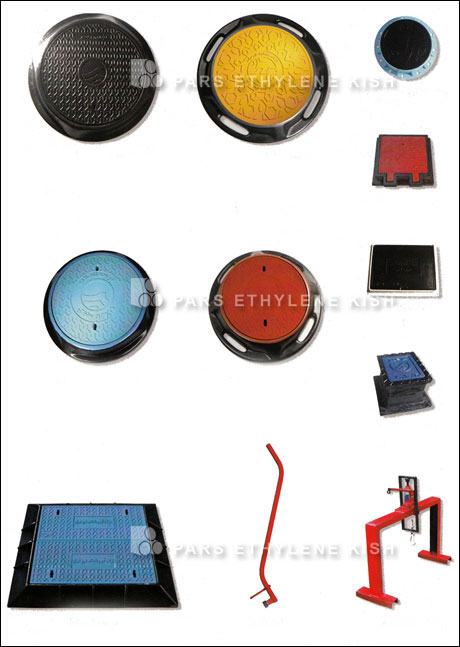