
Guide for the installation of single-wall HDPE pipes
HDPE Piping
Polyethylene pipes are capable of transporting drinking water, sewage, chemicals, slurries and hazardous wastes and gases. Nowadays, the use of HDPE pipes in the water supply networks is growing and managers of executive projects use polyethylene pipes instead of other types of pipes in most cases. The strength and durability and ease of installation of polyethylene pipes and polyethylene Fittings have are effective in this decision making by executives.
1 - Pipe cutting
2 - Cleaning the pipes and fittings
3 - Installation of pipes and fittings
4 - Installing the valves and accessories
5 - Clamps and concrete harnesses
6 - Preliminary burying of installed pipes
7 - Cleaning the pipelines
8 - Hydrostatic test of installed pipelines
9 - The test result
10 - Completion of burying the installed pipes
11 - Other general technical specifications of polyethylene pipes
1- Pipe cutting
In HDPE Piping there are cases where a piece of pipe shorter than the existing pipe branch is needed. In this case, the piece of pipe must be created by cutting part of the existing branch. The pipe cutting should be carried out in such a way that the ends of the pipe are thorough and safe and care should be taken not to damage the pipe.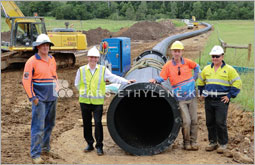
The cutting section of the pipe should be completely perpendicular to the pipe axis. To cut the pipes, do not use a large-teeth sawblade (carpentry saw). It is recommended to use a small-teeth saw (hacksaw) for cutting polyethylene pipes up to a diameter of 100 mm. For cutting larger pipes, machines and special tools shall be used for cutting plastic pipes. When cutting, to keep the pipe constant, clamps should not be used, as the operation of the clamp causes the pipe to collapse and the contact place will be damaged. When working with a cutting machine with the special tool of polyethylene pipe, it is necessary to comply with the instructions and recommendations of the manufacturer of the equipment on how to use these equipment and safety tips.
To cut the pipe, it is necessary to use devices that minimize the cutting chips. After finishing the cut, it is necessary to use the appropriate file to flatten the cut surface and remove all the cuttings and chips to be ready for butt weld.
2- Cleaning the pipes and accessories
Before installing, the interior and exterior surface of each and every branch of the pipe and its accessories must be cleaned completely by a clean and dry piece of fabric.
3- Installation of pipes and fittings
The contractor is obligated, by observing all the above items, to determine the pipes to be installed in the trench according to the appropriate number of branches and in the required quantity and, as the case may be, based on related items under the supervision and approval of the consultant engineer and mount them along with the trenches in the order in which they must be installed. The butt-weld joints of pipes and fittings must be carried out outside the trench. To ensure this, the contractor must provide lumbers of sufficient size, width and length at the workshop. These lumbers must be placed at a certain level on the trench and in a vertical direction along the trench. Then, the branches of the polyethylene pipes which are supposed to be welded to each other should be laid free on the lumber so that the axis of the two branches of the pipe are in the same line; under each branch of the pipe, sufficient number of lumbers should be placed at a distance to prevent the curvature of the pipes due to their own weight. Dimensions, number and distances of the lumbers depend on the diameter, length and weight of the branches of the pipes that are to be installed in the desired direction. When transferring pipes and fittings to these lumbers, it must be ensured that no waste material has entered into the pipe and its accessories. Once each pipe branch and any of its accessories have been placed on the lumbers, they must be immediately examined. It should be ensured that the pipe is clean and free of foreign objects.
The contractor can divide the piping operation in the desired location into some sections according to local conditions and facilities, and determine the number of branch pipes and accessories that are intended to be connected to each piece at each section, along with the dimensions, number and spacing of the lumber and act based on them after receiving the approval of the consultant engineer.
The connection procedure in various methods is described in clause 2.6.3. To facilitate the work with a special butt-welding device, the contractor can temporarily install a larger lumber frame on the trench at the place of connection of the pipes and up a special welding device on the timber. The connection operation should start from one side of the path and the connections are carried out one after the other, so that all the connections between the pipes and fittings are installed on the same path. The pipes and fittings that are connected and integrated to each other, as described above, form a piece of pipeline, which should be placed slowly in the trench. For this purpose, suitable machinery must be used at certain intervals along this pipeline, and, in front of each machine, the pipeline section must be hooked up by the belt that has passed from beneath the pipe and attached the crane. In this case, the cranes raise the pipes to separate the pipeline from the lumber and the lumber are then release. Then, the lumbers should be removed one after the other and the pipeline should be slowly placed in the trench by the crane. If the end of the pipeline has does not end into the conversion of the polyethylene flange, and it is intended to be connected to the pipe line from the next stage of the operation, the end of the pipeline unit shall not be placed inside the trench, but the end of this pipeline piece shall remain on the lumber laid on the trench and the connection operation of the pipeline segmentation shall be performed as in previous section. Keeping out the end of a piece of the pipeline as described, is possible when the length of the pipeline section and the pipe diameter are sufficient to allow the pipeline to have sufficient flexibility to bend. In pipes of a small diameter and relatively low weight, instead of using a machine, the pipeline can be arranged slowly into the trench with the help of several workers, each having a strap that passes beneath the pipe.
4. Installing the valves and accessories
If the connection of the valves to be installed in the polyethylene pipe line is of a flanged type, installing these type of valves is the same as installing valves in other pressure pipes. If the connection of these valves is of a different kind, then a polyethylene conversion that converts this connection to a flange connection can be used. The flanged interface parts are described in the accessories section.
5- Clamps and concrete harnesses
The clamps and concrete harnesses of pipelines of the pressure polyethylene pipelines are similar to the clamps of other pressure pipes, which are described in the section on common points of pipes and other parts of this collection.
6 - Preliminary burying of installed pipes
Before the hydrostatic test of the installed pipelines begins, it is necessary to bury the pipe in appropriate amount of soil so that the pipeline remains fixed in place and does not move as a result of the internal pressure during the tests. Considering that during the hydrostatic test of the pipeline, all joints should be visible in the valves and accessories so that leakage can be easily found in case of leakage of water. So the burying before the hydrostatic test should be done so that the connections and accessories and valves are visible. Burying carried out in this way is called a preliminary burying.
The preliminary burying is defined in the chapter of common points and in figure one. The contractor is obligated to inform the Consultant Engineer before the preliminary burying regarding the location of all connections and accessories and valves, so that the Consultant Engineer places the pipelines by taking into account these points and determines the places of pipeline that are allowed to be buried by paying particular attention to the types of connections, valves and accessories and communicate them to the contractor. The consultant engineer will determine these locations so that the body of each branch of the pipe is placed under the preliminary burying, but its connections are outside the preliminary burying. In the preliminary burying, it is necessary to observe the notes related to the type of foundation that is determined for the pipeline operation. The preliminary burying must, as far as the pipe is touched, be carried out with the same materials as those in the PVC pipes for bedding and backfilling. The rest of the preliminary burying should be carried out in accordance with the layout of the design. Preliminary burying should fill the surrounding parts of the pipe and be uniformly applied in several layers. The minimum burying height should be 30 cm and, in special circumstances, this minimum value will be applicable according to the design specifications and necessary measures.
7. Cleaning the pipelines
General pipeline washing should be carried out with clean water with chlorine at a concentration of injection into drinking water after completion of the test and disinfection. For this purpose, drinking water should be used (by controlling and adjusting its chlorine content) from the supply source. The amount of chlorine used for general washing is three grams per cubic meter, but it should never be less than 1 gram per cubic meter. In addition, due to the presence of high chlorine water in the disinfectant line, washing the entire line can be done immediately and at most within 24 hours after completion of the general testing and disinfection of the pipeline. General wash of the pipelines can be done simultaneous with disinfecting the line. To this end, after disinfection of the pipelines and water-supply networks, it is possible to reduce the concentration of chlorine in water used to disinfect the pipelines by gradually adding water with very low chlorine concentration, and gradually directing to the lines and networks in operation. Possible damage to the environment caused by water drainage with high chloride concentrations is avoided, but care should be taken to ensure that the injection of water with very high chlorine concentrations into the lines takes place very gradually and imposing sudden shock shall be prevented.
8. Hydrostatic test of installed pipelines
Hydrostatic test of polyethylene pipelines under the same pressure takes place like what was said in section 2.5.23 regarding the hydraulic testing of PVC pipelines. In the hydrostatic test of polyethylene pipes, in addition to the similar items for PVC pipes, the sensitivity for removing all the trapped air inside the pipeline is mandatory. The reason for this is the presence of a viscoelastic property in these pipes. This means that after applying the internal pressure, creep might be observed in the pipe wall and the internal pressure will then change. When the polyethylene pipe is under test pressure and the pressure supply pump is stopped, the pressure will gradually decrease inside the pipe. Even in the case of a piece of pipe that has been100% sealed, this pressure reduction will happen due to the viscoelastic properties of the pipe and the pipe’s creep. This reduction in pressure is non-linear, that is, at the start of the operation, the amount of pressure drop will be more and gradually stabilized.
The test pressure is at most 1.5 times the nominal pressure of the pipeline, but in special circumstances, the consulting engineer may reduce this amount to 1.5 times the work pressure of the pipeline. Polyethylene pipes should be tested in lengths proportional to the diameter and local conditions. The length of the pipe under test in small-diameter pipes is about 800 meters and it shall be less than that in pipes with greater diameter.
If the heat of the polyethylene pipe is more than 30 ° C, it should not be subjected to a hydrostatic test.
9. Test result
- After ending the pumping into the pipeline under pressure and after one hour, the test result is accepted if the amount of water required to supply the pressure to the initial value, does not exceed 3 liters per each kilometer of pipeline for every 25 mm internal diameter of the pipe and for every 3 atmospheres of test pressure in 24 hours.
- The duration of the test should also be inquired at the time of preparation of the pipe from the manufacturer.
- If the pressure drop is significant during the test time, and practically no water leakage is observed, it means that the amount of air trapped in the pipeline is high; this air should be discharged, and the hydrostatic test shall be rerun.
- If an unauthorized leakage is shown during the test, the mechanical accessories and then polyethylene welds should be checked and, after fixing the bugs, proceed with a re-test.
- After the test, the pressure inside the pipe should be gradually reduced to reach the pre-test condition.
If, for any reason, a re-test is desired, a reasonable interval should be considered between the two tests. This interval in any case should not be less than 5 times the length of time the pipe was under test.
10 - Completion of burying the installed pipes
After completing the hydrostatic test of the installed lines and fixing the defects, if the installed lines are accepted by the consultant engineer, the contractor is allowed to continue and complete the burying operations inside the trench, so that the trench is filled with dust and earth filling is appropriately condensed.
The contractor, after obtaining the permission of the consultant engineer, is obliged to bury the pipeline as follows:
1 - Parts of the pipeline at the location of the connections and valves that are kept open for the hydrostatic test shall be submerged with good quality dust, such as those defined for the preliminary burying.
2 - With the good quality soil which is accepted by the consultant engineer, continue the earth filling operations inside the trench in 15-cm thick layers and compress each layer up to 90% of the proctor until the surface digits of the final burying reaches a degree that the consultant engineer has determined based on the type and characteristics of the pavement layers. Pavement layers means a covering of suitable materials (such as asphalt, concrete, pavers) which is to be executed on the surface of the trench internal burying, so that the resulting figure is equal to the road or street.
3 - The contractor may, for the purpose of compacting the final earth filling into the trench, obtain the desired density by flooding the trench, instead of using the rolling technique, provided that in this regard, the approval and authorization of the consulting engineer are obtained. In these cases, the thickness of the submerged layers in the trench can be more than 15 centimeters.
4 - In cases where the pipeline which is the subject of the operation is installed in a passage that is subject to heavy vehicle traffic, the thickness of the soil cover of the pipe (from the crown of the pipe to the underpasses of the pavement) shall not be less than 60 cm. However, in the case where the passage is subject to lightweight vehicles, 30 to 45 centimeters of soil on the pipe is enough, provided that there is also control over the depth of frost.
11 - Other general technical specifications of polyethylene pipes
In compressed polyethylene pipelines, pipeline disinfection operations and pipeline general washing are similar to those in the section of common points of piping.

