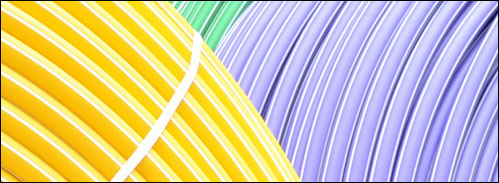
The Benefits of Polyethylene vs. Traditional Materials in Water and Wastewater Pipe Applications
Much of the U.S. pipe infrastructure is in poor condition and deteriorating further each year. Water and wastewater infrastructure in most areas is anywhere from 50 to 100 years old and has met or exceeded its intended life expectancy. Replacements and repairs made in recent years are only the first drops in the bucket – there’s plentymore to come.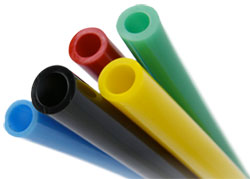
The U.S. Environmental Protection Agency (EPA) has projected that unless cities invest more to repair and replace their water and sewer systems, nearly half of the water system pipes in the United States will be in poor, very poor or “life elapsed” status in the next three years. Many of these systems are already in poor condition.
According to a recent American Water Works Association (AWWA) survey of 46 jurisdictions, including 43 states, there is an average 16 percent “unaccounted for” or “unbilled” water leakage, with some leakage as high as 50 percent.
If repairs are not made to the water and wastewater infrastructure in the United States, water utility customers might see water rates increase significantly. Municipalities are faced with the significant challenge of finding a cost-effective solution.
The good news is that the enhanced performance properties of polyethylene (PE) pipe offer a cost-effective solution.PE offers improved life-cycle performance with many benefits, including lower installation costs, reduced water leakage, corrosion resistance and reduced maintenance over the lifetime of a pipe infrastructure system.
Life-Cycle Performance
Reliable and efficient piping systems are essential to everyday life. Today’s pipelines are made from a variety of available materials ranging from the traditional – metal, concrete and clay – to plastics. However, some traditional pipes are losing treated water every day from cracking and corrosion. When specifying pipe material for a rehabilitation project, it is important to factor in several performance benefits over the entire product life-cycle of a water and wastewater pipe system.
Increased Flexibility for Ease of Installation
One of the first factors to consider is the cost to purchase the pipe material and install the pipe system. From a material and actual installation cost perspective, polyethylene pipe can be significantly less expensive than traditional materials, such as steel, depending on the location and installation method. In fact, at a recent installation in a major U.S. city, polyethylene pipe was found to be more cost effective. Polyethylene pipe, 12 inches in diameter, was approximately $15 per foot, while the same diameter pipe made from steel cost more than $30 per foot. In addition, the 12-inch polyethylene pipe cost approximately $70 per foot to install vs. more than $600 for steel pipe – a savings of almost $2.8 million per mile. This difference in installation costs between polyethylene pipe and pipe made from more traditional materials could be attributed to less intrusive installation options available with polyethylene pipe.
While there are the obvious monetary costs associated with installing pipe infrastructure, there are also societal costs, including soil displacement, surface restoration, traffic congestion and social disruption. High-performance PE pipe provides excellent pipeline flexibility needed for trenchless and other cost-effective and less intrusive installation methods. Trenchless installation technologies usingPE pipes, as opposed to traditional materials and installation methods, can minimize social disruption and reduce construction costs over open trench methods. A good example of a popular trenchless technology is horizontal directional drilling (HDD).
According to the Plastics Pipe Institute (PPI), over the last 20 years HDD has experienced major growth, becoming a more widespread trenchless method for water and wastewater pipe installation. HDD minimizes surface and social disruption, saving associated repair costs by allowing contractors to excavate underground without difficult river and waterway crossings or reconstructing paved surfaces such as highways, roads and sidewalks after digging open pipe trenches. PE pipe has become one of the most commonly used materials for this increasingly popular type of drilling. The flexibility of PE pipe is important when new pipe is pulled by cable from on e end of a newly excavated tunnel to another. Flexibility also allows pipe to conform to earth movements due to earthquakes and ground shifts.
Higher Performance Properties for Longer Lifetime Potential
It is important to remember that the life-cycle costs of a water and wastewater pipeline infrastructure do not necessarily end after installation. According to a corrosion study performed by the Federal Highway Administration (FHWA) and NACE International, the estimated direct cost of corrosion on infrastructure
in the United States is $36 billion annually and indirect costs are estimated to be at least twice that. The potential savings in direct and indirect replacement and rehab costs offered by the performance properties of PE pipe is tremendous.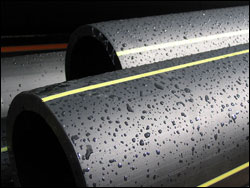
With recent advances in materials science and stricter performance standards, there is a range of PE pipe grade materials suitable for water and wastewater applications. This includes pipe made from high-performance resins, such as bimodal high-density polyethylene resins. PE pipe made from materials on this higher end of the performance spectrum meet or exceed current ASTM PE4710 standards. In addition to resistance to long-term slow crack growth, these bimodal HDPE resins also allow for downgauging a pipe’s wall thickness, thus reducing the material costs of the pipe. In water and wastewater applications, these advanced materials can provide longer overall life potential. For example, high-performance bimodalPE pipe made from resins offer resistance to slow crack growth, a critical property for long-term field service life. Bimodal polyethylene pipe also possesses resistance to rapid crack propagation against third-party damage and impact, as well as long-term performance. An inherent performance benefit of working with PE pipe is that polyethylene is resistant to most chemicals and does not corrode – a concern for underground water and wastewater pipe that comes into direct contact with corrosive materials in soil and water – saving money in rehab and replacement costs. More durable pipe using advanced materials means the potential for decreased maintenance cost over the lifetime of a water and wastewater infrastructure system.
With the declining condition of the U.S. water and wastewater infrastructure system, water utilities will most likely continue to experience pipe failures. With this in mind, the underground construction industry has a clear need for pipe materials that offer longer pipeline life expectancy, greater pipeline integrity
and durability, lower total installation costs and environmental advantages over traditional pipe materials for rehabilitation of the nation’s water and wastewater pipeline infrastructure.
Reliable, leak- and corrosion-free pipeline infrastructure is attainable. Due to recent advances in materials science, various high-performance polyethylene pipe materials are available, offering municipalities an unprecedented opportunity to cost effectively replace existing water and wastewater systems with longer lasting alternatives that meet their performance needs. The challenge is to deliver the material performance required today, while also ensuring future generations are not saddled with the same rehabilitation issues we are facing now.
Source: Heather Turner, North American Market Manager for Plastic Pipe, The Dow Chemical Company
|