Manufacturing Process of Polyethylene Tape
Polyethylene tape is a versatile adhesive tape widely used in multiple industries for its outstanding properties, including corrosion resistance, durability, and flexibility. It is a critical component in corrosion protection for pipelines, packaging, and sealing applications. In this comprehensive guide, we will delve into the fascinating manufacturing process of polyethylene tape, exploring the various steps involved in creating this essential product.
1. Raw Material Preparation:
The journey of polyethylene tape begins with raw material preparation. The primary ingredient used is polyethylene resin, which is derived from petroleum. Polyethylene is a type of thermoplastic polymer known for its excellent mechanical properties, chemical resistance, and low density. There are several types of polyethylene available, such as low-density polyethylene (LDPE) and high-density polyethylene (HDPE), each with distinct characteristics suitable for specific applications.
The polyethylene resin is processed to achieve the desired properties for the tape. The resin may undergo blending with other additives to improve its flexibility, strength, and adhesion capabilities. The proper choice of additives and resin grade ensures the final polyethylene tape meets the required performance standards.
2. Extrusion:
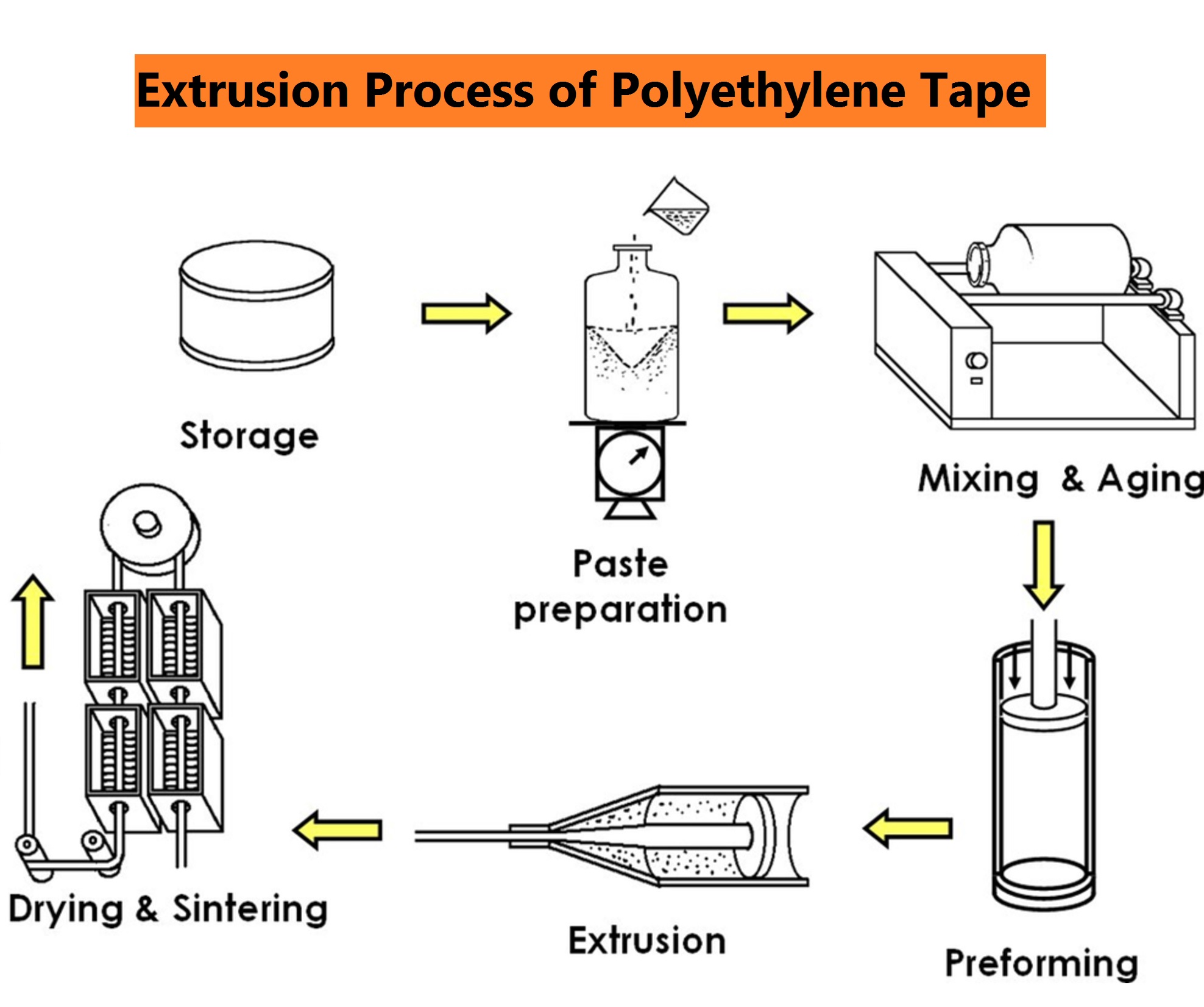
Extrusion is the initial step in the manufacturing process of polyethylene tape. The polyethylene resin pellets are fed into an extruder, where they are heated and melted. The molten polyethylene is then forced through a shaping die, forming a continuous thin film of the desired width.
The thickness of the tape is controlled by the speed at which it is pulled from the extrusion process. This step is crucial, as it directly influences the tape's mechanical properties and determines its suitability for specific applications.
3. Primer Coating (optional):
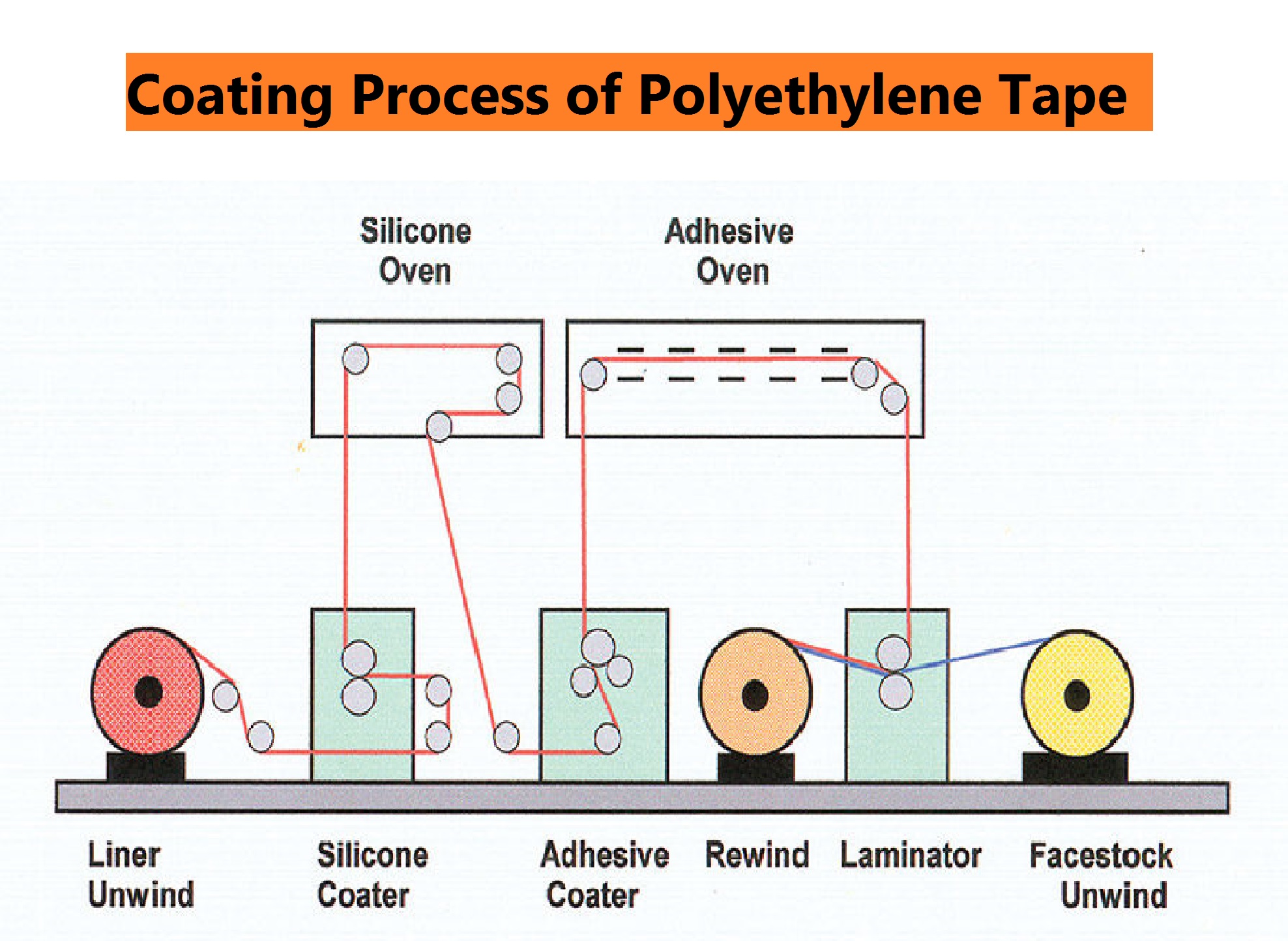
In certain applications, especially for pipeline corrosion protection, a primer coating may be applied to the surface of the polyethylene film. The primer enhances the adhesion of the subsequent adhesive layer to the pipe surface, ensuring a secure and long-lasting bond.
The primer typically contains a blend of resins, solvents, and additives designed to promote adhesion to both the polyethylene film and the substrate. This optional step is essential for ensuring optimal corrosion protection, especially when the tape is used for buried or submerged pipelines.
4. Adhesive Coating:
One of the most critical steps in the manufacturing process is the application of the adhesive layer. The adhesive is responsible for creating a strong and durable bond between the polyethylene tape and the surface it is applied to.
Various types of adhesives can be used, depending on the intended application and performance requirements. Commonly used adhesive types include rubber-based adhesives and acrylic-based adhesives. Rubber-based adhesives offer excellent tack and initial bonding strength, making them suitable for various surfaces. On the other hand, acrylic-based adhesives provide superior aging resistance and perform well under extreme temperature and weather conditions.
The adhesive is applied to the polyethylene film using a coating station, where precise control is essential to ensure an even and consistent layer. The thickness of the adhesive layer is also a critical factor, as it determines the overall bond strength and tackiness of the tape.
5. Drying and Curing:
After the adhesive coating process, the polyethylene tape enters a drying and curing oven. The oven subjects the tape to controlled heat, which serves two primary purposes:
-
a) Solvent Removal: If the adhesive used is solvent-based, the drying process eliminates any remaining solvents, leaving behind a solid adhesive layer. This is crucial for achieving a strong and reliable bond.
-
b) Curing: The curing process is essential for the adhesive to attain its final properties, including improved bond strength and resistance to environmental factors. The curing time and temperature depend on the type of adhesive used.
6. Cooling and Inspection:
Following the drying and curing process, the polyethylene tape is cooled to room temperature. Cooling ensures that the tape maintains its structural integrity and adhesive properties. Subsequently, the tape undergoes thorough inspection to verify its quality and adherence to manufacturing standards. This inspection includes assessing dimensions, adhesion, and visual appearance.
7. Slitting and Winding:
Once the polyethylene tape has passed inspection, it moves on to the slitting and winding phase. The tape is slit into narrower rolls of the desired width, tailored to specific customer requirements. These rolls are then wound onto large spools or cores.
The winding process must be precise to prevent wrinkling or damage to the tape. Proper winding ensures the tape remains in excellent condition during storage, transportation, and application.
Conclusion:
Polyethylene tape is a versatile and indispensable product, serving diverse industries with its exceptional properties. The manufacturing process involves several critical steps, from raw material preparation to winding the finished product. The careful selection of polyethylene resin, the application of the appropriate adhesive, and controlled curing are essential factors in producing high-quality polyethylene tape.
With its excellent corrosion resistance, strength, and flexibility, polyethylene tape continues to play a vital role in protecting assets and ensuring the integrity of pipelines, providing reliable packaging solutions, and serving various sealing applications. As technology advances, manufacturers continue to refine the manufacturing process to meet evolving industry demands and deliver even more innovative polyethylene tape products.
Read More: