Pipe Bursting Integral To Base Rehab Project
A pneumatic pipe bursting system saved time and money during repair of pipeline infrastructure at McChord Air Force Base
Replacement of an aging pipeline at McChord Air Force Base (AFB), Tacoma, Washington, was made simple when Seattle-based Pape & Sons Construction used a pneumatic pipe bursting system to repair failing concrete sewer pipe.
Through trenchless processes like pipe bursting are nothing new in Europe, American contractors, engineers, and municipalities are still discovering the economic and social benefits of these tools.
McChord expressed interest in using non-traditional methods such as trenchless technology for the repair
A Trenchless Solution
Pape & Sons investigated the use of pipe bursting. The McChord job had all the right components: tree root intrusion in 30-year-old concrete duct, difficult soil to excavate, close proximity to housing, and extensive surface structure such as brick divider walls and sidewalks.
The utility contractor sorted through sales information, real-world results, and interviewed more than 20 equipment manufacturers, contractors and pipe suppliers before deciding to go with a pipe bursting system.
A Grundocrack pneumatic pipe bursting system from TT Technologies, Aurora, Ill., and the model PCZ 180 7-inch tool was ordered for the pipe rehabilitation.
The Pipe Bursting Process
The pipe bursting process incorporates preparation of an entry pit at one end of the
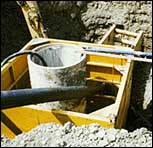
failed pipe section where a pneumatic pipe bursting tool and expander are positioned at the pipe opening. A steel cable emanating from a winch located at the exit point is attached to the head of the tool. The winch provides constant tension, helping to guide the tool. The bursting tool is then launched directly into the old pipe.
The combined effect of the percussive action of the pneumatic tool and constant tension from the winch enables the tool to effectively burst through the decayed pipe. The expander ensures that all pipe fragments are safely compacted into the surrounding soil and out of the way of the new pipe. Attached to the back of the tool, the new polyethylene (PE) pipe follows into the bore. Because an expander is selected with the outside diameter of the new pipe in mind, a tight fit is guaranteed.
Specifically, the project involved replacing 4,900 feet of 6-inch concrete duct with 8-inch SDR 21 high-density PE (HDPE) pipe. The flexural qualities of PE pipe enhanced the pipe bursting process. The existing concrete duct was laid in 3.5-feet sections about 30 years ago. Runs of 100 feet to 325 feet were encountered for the replacement. The project was actually started by using a dig-in process, but then bursting took over.
"We were able to accomplish just one run in 2 to 3 days with the dig-in process. With the bursting method, we were able to do two runs per day," said Dick Harrod, a project manager for the contractor
Pipe Bursting Saves Money
Pipe bursting opens new windows of opportunities for improving infrastructure, because trench-and-replace construction can be so expensive that repairs are often put-off. The failing pipe then continues to further corrode, demanding the time and expense of more frequent cleanings.
Positive social factors are a key benefit in using pipe bursting. It allows highway traffic to flow as pipe is installed beneath pavement, and leaves yards, trees, and gardens intact when replacing lateral connections.
Because bursting takes less time to perform than open cutting, it requires minimal disruption to the public, reduces restoration costs, and generates greater savings for the owning company, Harrod said.
In the coming months, 13,000 feet of deteriorating concrete pipe in Mansfield, Washington, will be rehabilitated. Because of very flat terrain, Mansfield's present system has developed slow-flow characteristics that have been contributed to deterioration of joints in the 8-inch and 10-inch concrete pipe system.
Pipe bursting is expected to be the method of choice for that replacement, and because of its outstanding flow properties, HDPE pipe will take care of the slow-flow problem.
Based on the original budget specifying the trench-and-replace method, the entire trenchless rehabilitation project will save Mansfield an estimated $350,000.
source : tttechnologies.com