
Corrugated pipe factory
Producer of double wall corrugated pipes
Pars Ethylene Kish after doing lots of research and building on the knowledge of the managers and the research and development unit has managed to make a significant difference (innovative and creative) in production of double wall corrugated pipes , corrugator dies which has yielded to pipes with more resistance, higher quality and longer lifetime compared to the other samples in the country.
Important notes in the factory of double wall corrugated pipes
-
The extruders used in production of polyethylene pipes must be of credible and well-known European brands.
-
The production line must be equipped with modern and automatic control systems while production which reduce the probability of any error to zero while production of pipes.
-
The extruders and other instruments of the production line must be new.
-
Make sure of the marking on the polyethylene pipe and its being standard.
-
Storing, maintenance and transportation must be according to the standards.
-
The factories shall be located within well-known industrial complexes with unlimited access to the freeways of the country.
-
The factory environment and workplace shall be in good order and free of excessive elements.
-
The raw materials shall be kept in the shadow and away from moisture.
-
The raw material shall be injected into the extruders via silos.
-
The cooling system of polyethylene pipes
-
Side systems of production line (pool, electricity, compressors, etc.)
-
The system and procedure of controlling the dimension of polyethylene pipes during and after production of double wall corrugated polyethylene pipes
-
Quality control and laboratory unit
-
The storage location of polyethylene pipes shall have a smooth surface.
-
The conveying and loading method of polyethylene pipes shall be examined and in conformity with the instructions.
The abovementioned tips are important which should be particularly considered in the inspections of the factories producing polyethylene pipes.
The corrugated pipes manufactured by Pars Ethylene Kish company are also characterized by another property which is a protective wrapping on the coupling of double wall corrugated pipe. The wrapping, being very simple, acts as a protective belt and prevents the coupler from tapering in the junction of the pipes and also prevents fluids from permeating out. Another main defect of the corrugated pipes in the market is this very tapering and erosion of the pipes at the junction which degrades the performance of the transmission line severely.
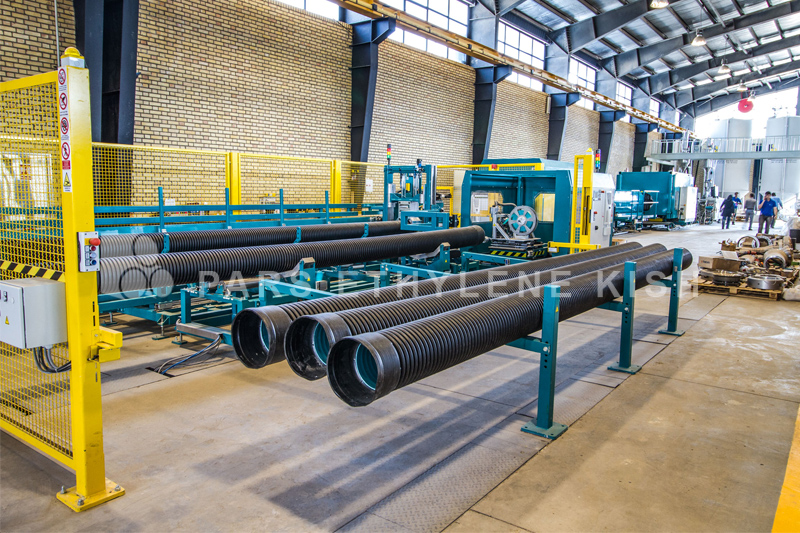
Outstanding properties of a factory producing polyethylene pipes:
-
Customer orientations is our motto and respecting the customer is a priority to us in relation with the customers.
-
The producer values the time of the customers and speed in provision of the best and high quality products and services is the goal of its efforts.
-
The producer must design, upgrade and supply its products according to the needs of the customers and their comments.
-
The producer must consider the human resources as the most precious asand the fundamental factor of organizational growth and excellence.
-
The producer must believe in teamwork.
-
The producer must seek its success in sustainable development and environmental protection and always consider it a value for itself.
Notable remarks regarding production of corrugated pipes:
In order to produce corrugated pipes, first the raw materials are melted at high temperature in the extruder through the extrusion process. Thermal adjustment in this stage is very important since in different thermal areas the type of the product and the polyethylene would be different (extrusion is a process in which the raw materials are poured in a die and applying pressure products with different designs are made). Then the resultant polyethylene passes through a tank and turns into the shape of a pipe. To create grooves and ridges on the outer surface of the pipe (corrugating the pips) this process is performed under vacuum situation and using rotatory and continuous dies. Thermal adjustment in this stage is important too. There are water nozzles at the end of the production line of corrugated wall for cooling of the output product. The quality control stages of the products are performed at the factory laboratory.

Production of corrugated polyethylene pipes is rapidly developing in technology, production process and the control while production. In addition to the abovementioned definitions, the production process of the corrugated pipes could be divided into 5 stages including:
- Preparation of the raw material
This is an important stage in the production process for it requires the collaboration of the staff in different levels. Preparation of the raw material starts with the purchase order and ends with making the mixture and transferring it to the extruder funnel. This stage is directly related to the production plans. This phase consists of: purchase order, receiving, storing and making the mixture.
Provision of the raw material:
The raw material used in the production process are approved by the employees in an operational team as production, guarantee of quality and purchase, based on technical specifications of the raw material, the required criteria for product standards, reliability of the supplier and quality control tests of the raw material and the products made from it. In case the raw material would possess the desired quality, it will be ordered and purchased.
Receiving and storing of the raw material:
The raw materials are sampled and evaluated by the quality control agent upon arrival at the factory. In case that the sent shipment was in conformity with the requested specifications based on the specs out on the specifications documents of the products and the bill of lading, the quality control agent will perform the standard tests on the samples to determine the conformity of the shipment and to provide report. In case of any discrepancy in the specifications of the raw material with the relevant standards, the shipment will be returned.
The tests performed on the raw materials are as follows:
- melt flow index (MFI)
- density test
- oxidative induction times (OIT)
- Humidity test
- soot dispersion test
- Extrusion
In the extrusion stage of thermoplastics, the polymers are melted by the heat created inside the extruder. Melting of heavy polyethylenes is controlled by precise adjustment of the thermal profile in different areas based on the polymer type which results in optimum pressure in the extruder output. This task is performed by the production personnel according to the guidance instructions for quality control and method.
- Corrugation
After the extrusion, the polyethylene has passed through die and gets the pipe shape at the die output. Then the corrugating process of outer surface of the double wall pipe is performed by applying die and vacuum, while the inner surface of the pipe is still smooth. Such molding process is continuously performed by corrugating rotary dies.
Based on type of the desired pipe, respective parts and dies are installed on the production line and during the production process, stabilization of thickness of polyethylene pipe layers, production speed and temperatures are adjusted at their optimum. The quality control agent performs the necessary controls on the final products to ensure the desired quality is achieved.
- Calibration
The cooling stage is essential for stabilization of the dimension in production of plastic pipes which is named as calibration and is different based on the pipe thickness and production speed. In order for cooling of the pipes, the water nozzles are used which are embedded all around the pipe along the calibrator. The water temperature of the cooling system is also under control.
- Confirmation and final product tests
In the final stage of the production process, the corrugated pipe is sampled and the quality control unit performs the respective tests to determine whether the final product is in conformity with the required specification and also optimizes the adjustments.
The production process, the stages from stage 2 to 5 are controlled by the production personnel and quality control agent. Finally, the quality control unit samples the products and does the final confirmation according to the standard tests.
Quality control of corrugated pipes
The quality control laboratory is one of the main and vital sections of any factory which is producing polyethylene pipes and fittings. The laboratory equipment should be always inspected and calibrated and the laboratory must have NACI 17025 certificate.
Polyethylene corrugated pipes are inspected and controlled via two aspects. In the first one the corrugated pipes undergo superficial inspection by quality control personnel in terms of length, diameter, profile shape, roughness of inside of the pipe, weight of each meter of the pipe and so on. Then they are sent to the quality control laboratory which is equipped with developed laboratory instruments for more examination. The quality control unit has managed to supply its products with high quality to the domestic and foreign markets by performing precise tests on the products according to both national and international standards.
The tests are performed according to DIN-16961, ISIRI-9116 and EN-13476 standards.

List of standards for double wall corrugated pipes:
The following tests are performed on double wall corrugated pipes:
-
Density (according to ISIRI 7175-5 standard)
-
Melt flow index (according to ISIRI 6980 standard)
-
long-term ring stiffness (according to DIN 16961 standard)
-
short-term ring stiffness (according to DIN 16961 standard)
-
ring flexibility (according to EN 1446 standard)
-
measurement of soot volume (according to ISIRI 7175-2 standard)
-
soot dispersion (according to ISIRI 7175-6 standard)
-
thermal reversion (according to ISIRI 7175-3 standard)
-
dimensional control (according to DIN 16961 and ISIRI 9116 standards)
-
Weld line elongation (according to EN 1979 standard) Sealing

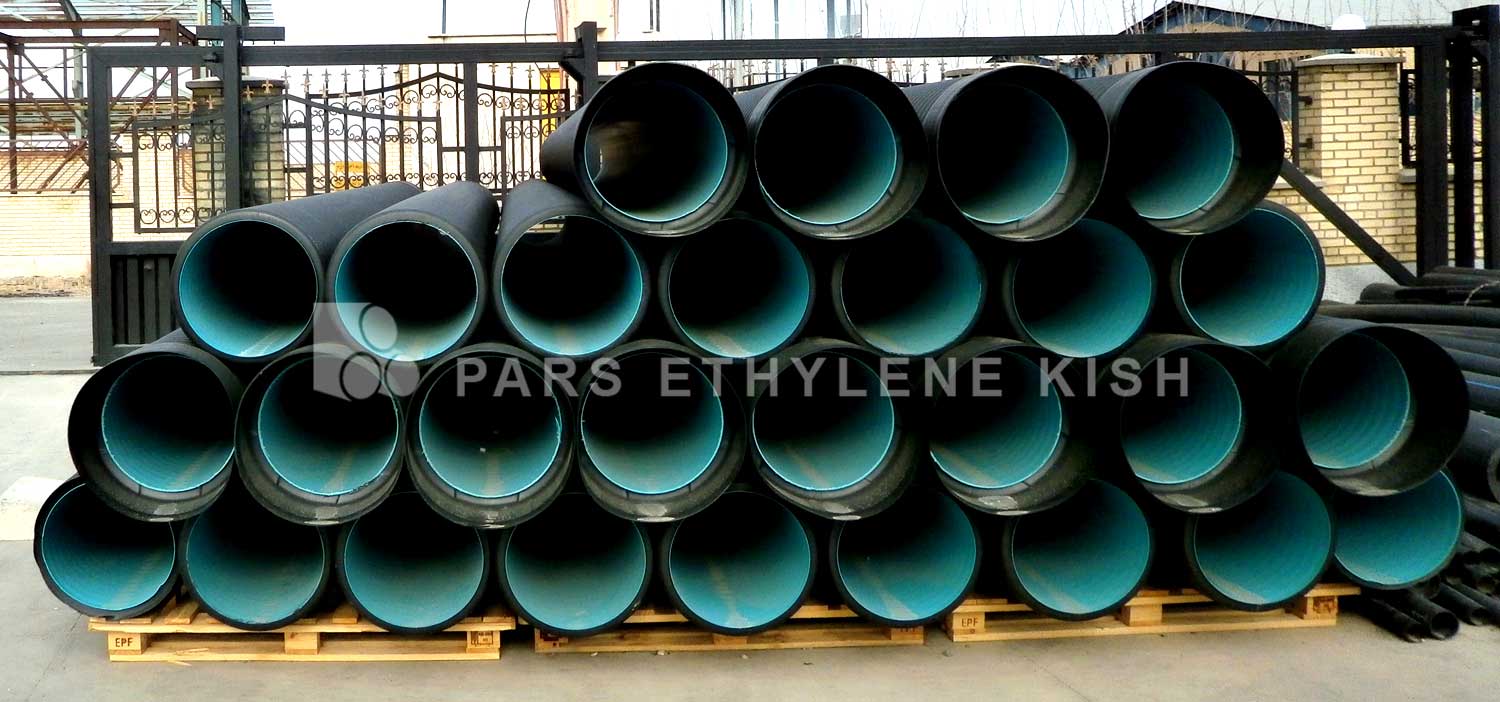

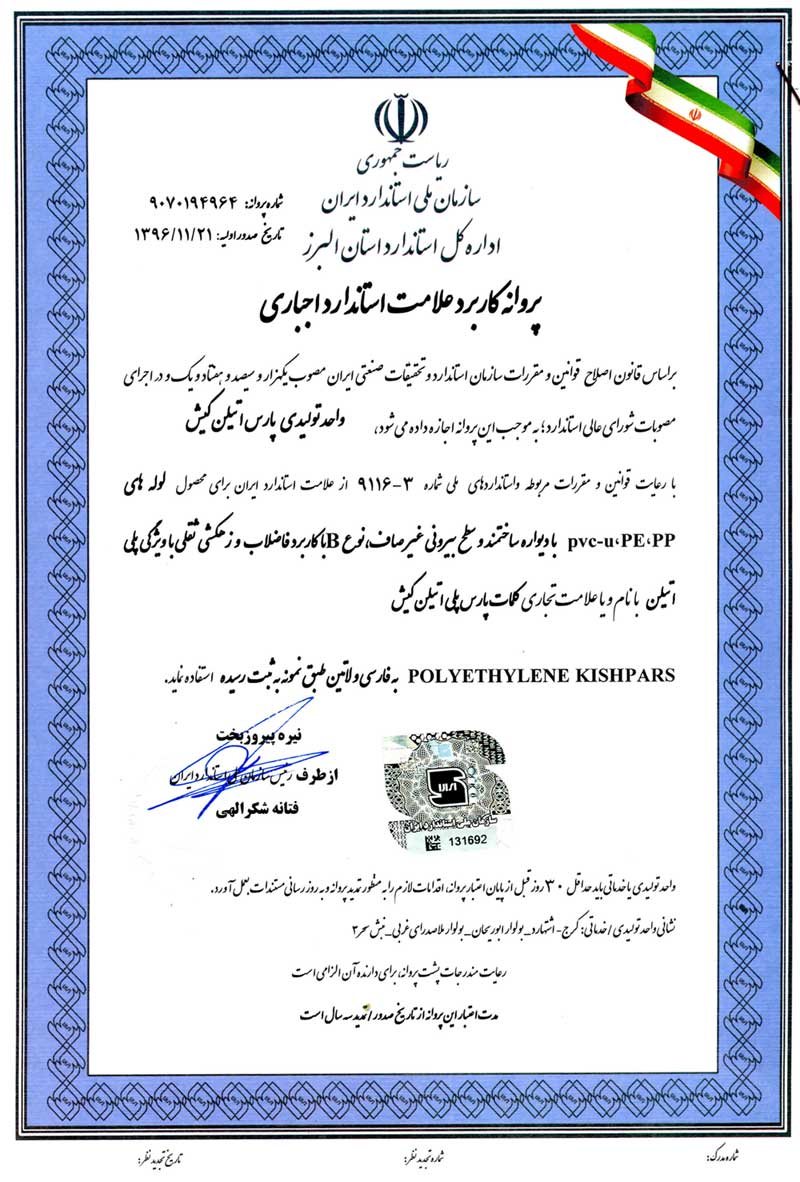