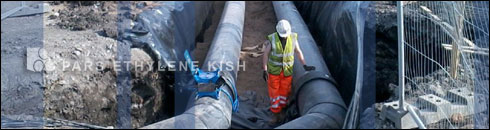
Polyethylene Pipe | HDPE PIPES
Polyethylene Pipe (PE pipe) has been used to transport fluids For nearly 50 years. Its ability to withstand harsh chemicals without corrosion and leak as well as the tight installation, polyethylene (PE) has been regarded as the ideal material for the gas industry. The continuing technological improvement of polyethylene materials has resulted in the rapid growth of numerous usages of polyethylene (PE) in both water and gas industries since the early ‘70’s. Polyethylene (PE) is now the material of choice. It is superb in resisting corrosion. Additionally, butt welding PE joints offer leak-free connection which outperforms any other competing materials in terms of reliability and longevity, not to mention the remarkable savings on the installation costs and life of the materials.
These improvements in PE materials resulted for the water industry to adopt it for its pressure transmission network. The improvements are mainly the development of pe80 and pe100. In this catalogue, pe100 will be the basis of the discussion, although some references will be made.
Polyethylene Pipe (PE100) high performance polyethylen
Polyethylene (PE100) is considered as the most heavy duty amongst other types of pe pipes. Compared to PE80 & PE63, PE100 is best used for water & gas mains with its maximum working pressure. It has enhanced toughness, higher permissible design strength and improved resistance to rapid crack propagation. “high strength” HDPE (PE100)pipes offer the water engineer substantial benefits in performance efficiency and economy of its use.
Pe100 pipes are also used in various applications such as:
-
Sewage pumping mains
-
Fire mains
-
Chilled water
-
Submarine pipe lines
-
Industrial and chemical applications
Why we choose polyethylene Pipe (PE Pipe)
Polyethylene pipe systems offer significant advantages over ductile iron, steel and cement systems. Some of its advantages are as follows: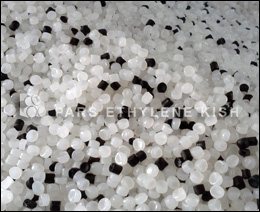
1.Corrosion resistance: polyethylene is basically chemically inert. This pipe system does not rust and corrode. This system resists chemical attack from aggressive soils. There is no need for protective layer or finishing process that is required.
2.Leak tight: butt fused joints create a homogenous system. The fusion weld for this system is very strong. Therefore, unlike ring type joints or the other mechanical jointing systems, there is no risk of leakage resulting from joint distortion.
3.Optimum flow rate: smooth inside pipe surface allows for a high hazen-williams “c” factor. “c” remains constant throughout the lifetime of the system due to an innate high resistance to scale and biological build up. Polyethylene (PE) is biologically inert.
4.Excellent water hammer characteristics to withstand surges: the inherent properties of polyethylene allow the system to significantly lower the effect of surges compared to pvc and ductile iron systems.
5.Flexibility: this system allows polyethylene pipes to be coiled and supplied in length of up to 200m for small diameter pipes. This feature is one of the many contributions to cost savings during the installation process.
6.Resistance to geological conditions: a polyethylene system has inherent resistance to ground temperature fluctuations and earth instability.
7.High strain allowed virtually eliminated failure due to freezing pipes.
8.Reduced installation costs.
9.Long track record of excellent performance, fast approaching to 50 years worldwide.
Advantage of polyethylene (PE100)
-
High impact and breakage resistance.
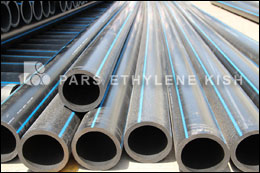
-
Very high resistance to direct sunlight (uv resistance for long time .this is supplied by ultraviolet light resistance agent mixed to the pe raw material.
-
There is no need to take protection precautions at the time of installation like cathodic protection.
-
Availability of connection at a place out of the trench.
-
Advantage of being not affected from earth movements like landslide , earthquakes , etc.
-
Pe pipes require less fittings for connection because they are elastic and in many place they do not require connection where the other types do. Because pe pipes are bendable
-
ith a radius of 20 times of its out diameter. The other pipe type do not have this advantage.
-
Advantage of mobilization of the pe pipe production facilities .this enable very big saving in transport costs for projects where large diameter pipes are required.
-
Advantage of higher durability & advantage of easy installation and transport without material loss.
-
Pe pipes do not require concrete block at the place like bending and tee separations.
-
Pe pipes do not require welding characteristics.
-
Very good adoption to earth movements.
-
Many different pressure resistance option , pe pipe can be produced resistant to 12 different pressure class from 2.5 bar up to 32 bar.
-
High resistance to chemical , not affected from corrosion , decaying and abrasion.
-
Advantage of perfect leak proof no crack no break and no deformation.
-
Advantage of safe application in irregular surface like sea, river lake passages at place where there sockets etc.
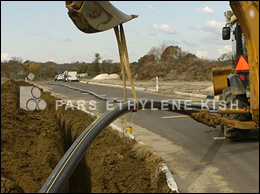
-
Availability of more than one connection method (butt welding. Electro fusion welding , push fit sockets etc.)
-
Advantage of having perfectly smooth internal surface because of this advantage of pe pipes in comparison to the other pipe types .this brings considerable saving in the overall cost of the line and the services costs.
-
Pe pipes have the advantage of very long service life under severe conditions.
-
Pe pipes are light in weight which enable the installation with high speed at places.
-
Pe pipes are elastic which is a big advantage during the earthquake or any other earth movements. This characteristics also big advantage in transport (coiling up to 125 mm diameter and in installation costs.
PE Welding
PE Manhole
PE Fitting
PE Pipe
Valve | PEX pipe | Push fit system | Plastic pipe | Polyethylene pipe
Water pipe | HDPE Pipe | Corrugated pipe | Spiral Pipe | PVC Pipe | Sewerage pipe
|