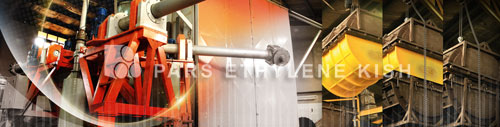
Production of Polyethylene Manhole
Production Line and Machinery of Polyethylene Manhole
Pars Ethylene Kish polyethylene manholes are produced by the largest and most modern rotary molding machines, Pars Ethylene Kish is the first and the largest industrial unit in the field of designing, producing and manufacturing standard polyethylene manholes in the country. The company, with the help of experienced staff in the polyethylene industry, has been able to achieve the technology of making rotary molding machines.
The polyethylene manhole production process involves five steps, making the pattern, making molds, melting materials, pouring materials and finally cooling. Polyethylene manhole production line of Pars Ethylene Kish is one of the most advanced and newest manhole production equipment in the world. Pars Ethylene Kish manholes are designed according to different needs and uses, and are national and international, and are produced using rotary molding technology (rotary molding).
The raw material is granular, which is initially converted to a powder by a pulverized mill with a special roller for the production of powder from polyethylene materials, and after the special molds attached to the rotary machine arms, was poured into the mold. Afterwards, the molds are rotated in a rotary kiln under high temperature and under precise time control, and after the exact time of heat shrinking, and at the end of the cooling process, the process is carried out.
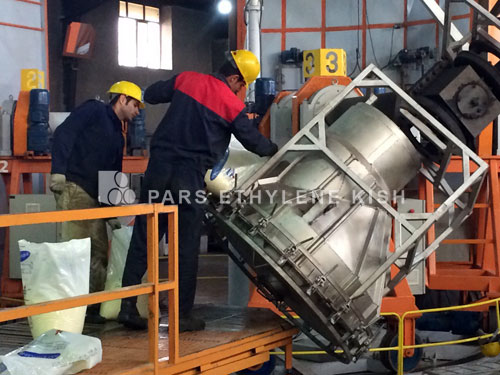
The above steps, which are completely summarized and in plain language, describe the production of polyethylene manholes, but the importance of mold and quality and mold design should not be easily passed. Polyethylene manholes are made with special molds. A rotary machine is composed of components: three or four flange arms, a cooling system, and two or more raw material loading stations and an output valve for the final product.
Polyethylene manhole production process with molding rotary
loading the manhole mold
At this stage, the mold, which is designed as a manhole (final product), is opened and a certain amount of powdered polyethylene material is cast in the bottom half of the mold. Calculate the amount of polyethylene based on the weight of the final piece and naturally the expected thickness.
Heating the manhole mold
After the mold is closed, the machine starts to work and the molding rotates around the two overs in the furnace.
In most cases hot melt furnaces are used to heat the mold. The heat of the furnace is transmitted through the wall of the mold to the polyethylene and causes the polyethylene powder to adhere to the inner wall of the mold cavity. At this stage, due to gravity, the polyethylene is continuously located in the lower part of the cavity of the molding, and this rotation to each of the cavity points allows for the coverage of some polyethylene material. The points of the mold that are supposed to be thicker on the piece should be more in contact with the polyethylene. Therefore, by changing the speed of the rotating axes of the molding on a rotary machine, the thickness can be controlled at different points.
The ratio of velocity (the ratio of rotation) is the velocity of the mold’s rotation spees in the main axis (arm) divided by its velocity in the axis (plate). The most common speed ratio used to produce components in this method is a ratio of 4 to 1. It should be noted that the rotational speed of the molding is relatively quiet over the two axes. Although the increase in the rotational speed of the mold may increase the production efficiency, the complexity of the shape of the piece and the large size of molds usually do not provide such a possibility.
During the heating cycle, the mold that is in the furnace is heated and the heat is passed through the wall to the polyethylene powders. This causes the powders to stick to the wall of the mold cavity and to each other. Therefore, a loose powder mass is formed adjacent to the wall of the mold cavity. As the heating cycle continues, the polyethylene powder mass coagulates gradually, and the air bubbles between the particles of the polyethylene powder become smaller and smaller. As long as the polyethylene powder is converted into a uniform melt, all bubbles fade away. It should be noted that these bubbles are not able to move to the surface due to the high viscosity of the melt, leaving only the place where they exist, to be smaller at the end of the heating cycle.
Cooling manhole mold
At this point the rotating mold will enter the compartment or cooling station. When the mold is cooled by the flow of air, polyethylene is also cooled down and the polyethylene manhole is formed.
Manhole drain from the mold
At this stage, the mold stops and the final piece, which is sufficiently cooled, is released by opening the half mold.
Step by step production of polyethylene manholes using rotational molding technology
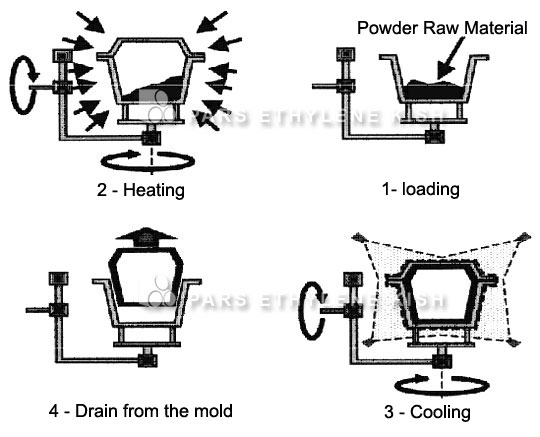
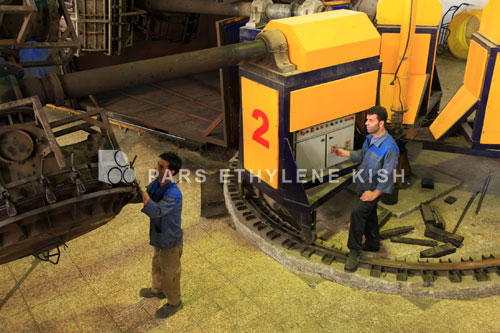
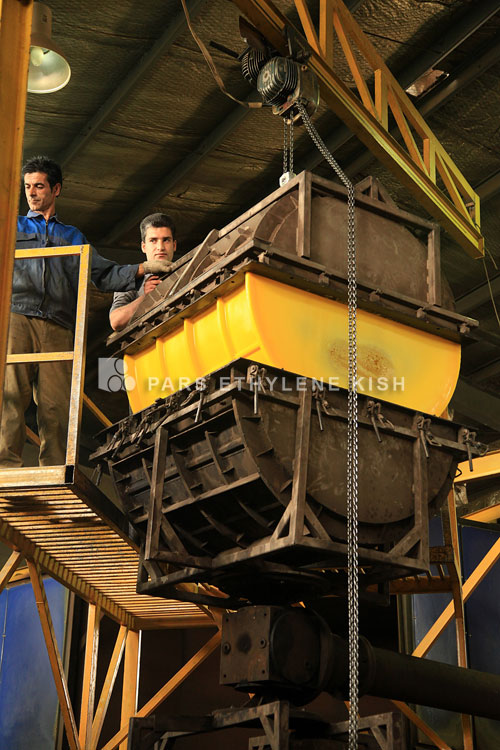
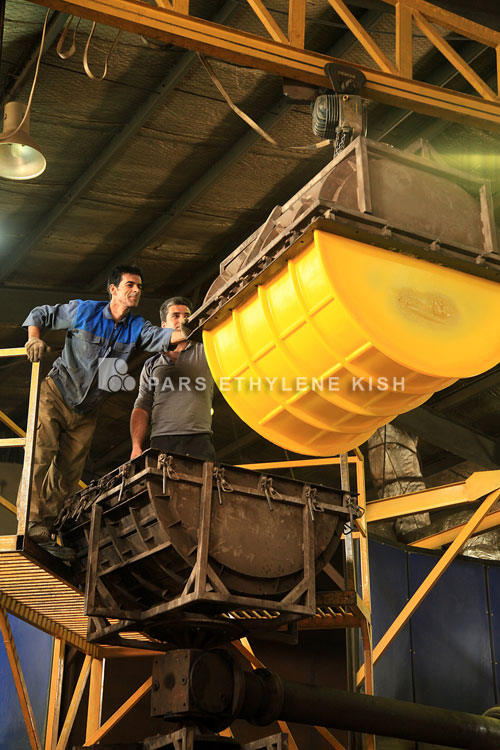